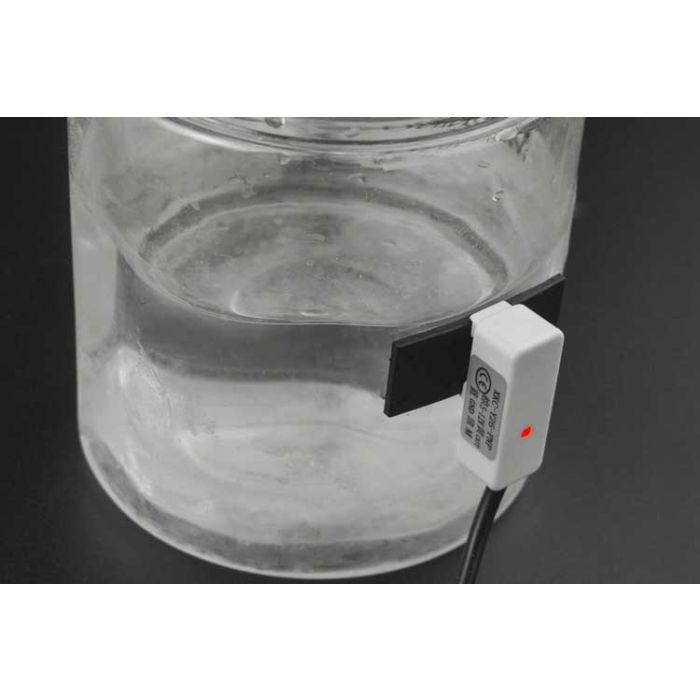
How Can Liquid Level Change Be Sensed by a Capacitive Sensor?
Accurate monitoring of liquid levels is a vital task in many industries, from automotive to food processing and chemical manufacturing. Knowing how much liquid is present in a tank or container can prevent overflows, improve safety, and ensure efficient use of resources. Among the various technologies available for this purpose, capacitive sensors stand out for their precision, durability, and adaptability. But how exactly do these sensors detect liquid level changes? Let's explore the science behind capacitive sensing and its practical applications.
How Do Capacitive Sensors Work?
Capacitive sensors operate based on changes in capacitance, a property determined by the electric field between two electrodes. Capacitance depends on the material between the electrodes, specifically its dielectric constant. Solids, liquids, and gases all have different dielectric constants, affecting how easily they allow an electric field to pass through. Since liquids generally have higher dielectric constants than air, capacitive sensors can detect variations in liquid levels by measuring these changes.
The Basic Principles of Capacitive Sensing
Capacitive sensing relies on three key steps:
-
Electric Field Interaction:
A capacitive sensor generates an electric field between two conductive plates or components. Typically, one is placed inside the liquid container as a probe.
-
Dielectric Constant Changes:
When liquid comes into contact with the probe, its high dielectric constant alters the capacitance between the sensor and the tank wall. This differs significantly from the capacitance when the probe is surrounded by air.
-
Signal Processing:
The sensor measures these changes in capacitance and converts the data into a readable output, such as a voltage, analog signal, or digital reading. This output corresponds to the liquid level in the container.
By continuously monitoring capacitance, capacitive sensors provide real-time updates on liquid level changes.
Practical Applications of Capacitive Sensors
Capacitive sensors are highly versatile and find use in a wide range of industries. Here are some examples of how they are applied:
-
Automotive Fuel Tanks:
These sensors are crucial for tracking fuel levels in vehicles, ensuring accurate readings even during motion. By measuring the changes in capacitance caused by the varying levels of fuel, they provide precise data to the vehicle's fuel gauge system. Additionally, their durability and reliability make them suitable for use in harsh automotive environments, where temperature fluctuations and vibrations are common. This ensures drivers have consistently accurate information about their fuel levels, enhancing safety and efficiency.
-
Industrial Applications:
Capacitive sensors are versatile tools used in industrial processes to monitor liquid levels in chemical processing plants and food production facilities. For example, they are commonly utilized to measure water, oils, and other liquids critical to production, ensuring consistent quality and preventing issues like overflow or shortages. Additionally, their ability to function in harsh environments, including extreme temperatures and chemically aggressive conditions, makes them reliable and durable for industrial use.
-
Water Management:
These sensors are integral to detecting water levels in reservoirs, tanks, and other storage systems, making them essential for efficient water use in agriculture and urban settings. Their high sensitivity and accuracy allow for smart water management systems that minimize waste while optimizing the use of this vital resource. For instance, in irrigation systems, capacitive sensors ensure that crops receive the exact amount of water needed to thrive, promoting sustainability.
-
Pharmaceuticals:
Capacitive sensors play a critical role in monitoring liquid reagents or medication solutions where precision is paramount. They provide accurate and consistent measurements, ensuring that certain pharmaceutical processes, such as drug formulation or the preparation of sterile solutions, meet rigorous quality and safety standards. Furthermore, their non-invasive design reduces the risk of contamination, making them ideal for highly controlled environments like cleanrooms.
Their adaptability to different environments and liquids makes capacitive sensors a preferred solution for modern liquid monitoring needs.
Advantages of Capacitive Sensors
Capacitive sensors bring several benefits compared to other liquid level monitoring technologies:
-
Accuracy:
Capacitive sensors provide extremely accurate readings, often with resolution levels down to millimeters, making them ideal for applications requiring precise monitoring in industries like pharmaceuticals, food processing, and energy production.
-
Versatility:
Capacitive sensors can handle a wide range of liquid conditions, including varying temperatures, densities, and dielectric properties. This makes them suitable for both industrial and scientific applications, as well as for use with corrosive or hazardous materials.
-
Durable and Low Maintenance:
Designed with robust materials, these sensors can withstand harsh environments, such as high-pressure systems or extreme temperatures. Their low maintenance requirements also reduce downtime and operational costs in long-term applications.
-
Non-Invasive Measurement:
These sensors can be installed on the exterior of tanks or containers, making them ideal for sterile environments or systems where direct contact with the liquid could interfere with processes or standards, such as in medical or laboratory settings.
-
Wide Compatibility:
Ultrasonic liquid level sensors are compatible with a variety of liquids, including corrosive substances, making them suitable for industries such as chemical processing and wastewater treatment.
-
Real-Time Monitoring:
These sensors provide real-time data, enabling quicker responses to changes in liquid levels and improving system efficiency and safety through instant alerts.
-
Energy Efficiency:
Ultrasonic liquid level sensors are designed to be energy-efficient, consuming minimal power during operation, which is particularly beneficial for battery-powered or remote systems.
Challenges and Considerations
While capacitive sensors boast many advantages, they come with a few limitations you should keep in mind:
-
Environmental Sensitivity:
Extreme temperature or humidity changes might influence sensor performance and require recalibration.
-
Liquid-Specific Calibration:
Different liquids have varying dielectric constants, so sensors need to be specifically calibrated for the liquid being monitored.
-
Tank Material Limitations:
Non-conductive tanks, like those made of plastic, work best for capacitive sensors, as conductive materials can interfere with the electric field.
Conclusion
Capacitive sensors are a powerful and reliable solution for detecting liquid level changes in a variety of industries. By leveraging their ability to measure variations in capacitance caused by dielectric constant changes, they ensure precise and efficient liquid monitoring. Whether it's keeping track of fuel in vehicles, ensuring optimal water levels in reservoirs, or maintaining critical measurements in production lines, these sensors have become an indispensable tool.
While they do require careful calibration and consideration of environmental factors, their precision, adaptability, and low maintenance make capacitive sensors a solid choice for modern liquid level sensing. For industries seeking both accuracy and reliability, capacitive sensors deliver on all fronts.