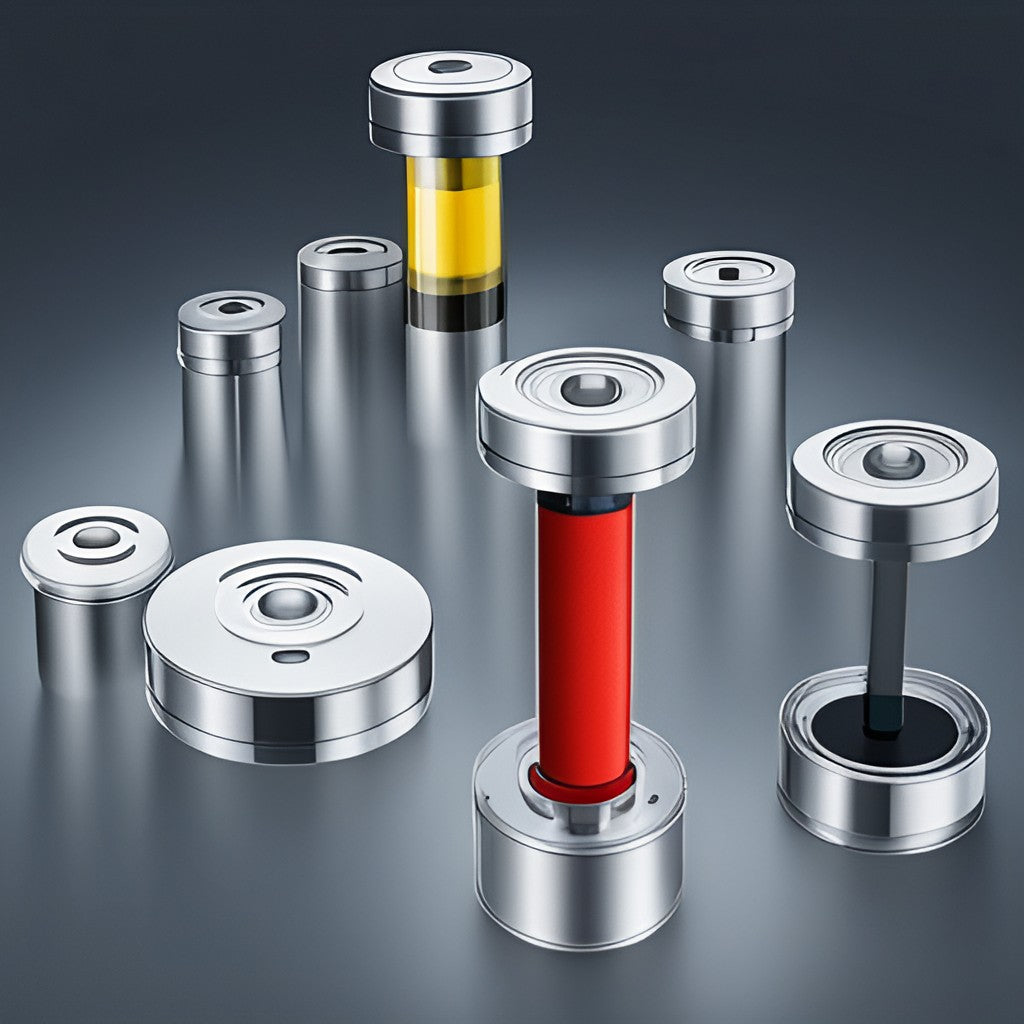
Navigating the Depths: The Comprehensive Guide to Liquid Level Sensors in Industrial Applications
In the vast sea of industrial applications, liquid level sensors emerge as critical navigational tools, ensuring operational efficiency, safety, and regulatory compliance across a myriad of sectors. This comprehensive guide aims to illuminate the technological foundations, diverse types, practical applications, and future projections of liquid level sensors, guiding industry professionals through the depths of this essential technology.

Technological Foundations of Liquid Level Sensors
At the core of liquid level sensing solutions lie three primary technologies: mechanical, electro-mechanical, and electronic sensors, each with unique mechanics and industry use cases.
Mechanical Level SensorsMechanical sensors, such as float switches, conductivity probes, and pressure sensors, rely on physical contact with the liquid. Float switches, for instance, move with the liquid surface, triggering an action when reaching a predetermined level. These devices are known for their reliability and straightforward design, making them suitable for a range of applications from simple water level indication to complex industrial processes.
Conductivity probes function based on the electrical conductivity of the liquid. By measuring the resistance between two or more points in a tank or vessel, these sensors can determine the presence or absence of a liquid at a specific level. This type of sensor is particularly useful in applications involving conductive liquids and is favored for its simplicity and cost-effectiveness. However, its application is limited in non-conductive or highly pure liquids, where alternative sensing technologies are necessary.
Pressure sensors, another subset of mechanical level sensors, measure the pressure exerted by a static column of liquid at a specific depth. This pressure is directly proportional to the height of the liquid, allowing for an accurate determination of the liquid level. These sensors are versatile and can be used in a wide range of liquid types and conditions, from water to highly viscous fluids. Pressure sensors are highly regarded for their precision and the ability to provide continuous level measurement, making them indispensable in many industrial scenarios.
Electro-Mechanical Level SensorsCapacitance and ultrasonic level sensors represent the electro-mechanical category, expanding the capabilities of level measurement. Capacitance sensors detect level changes through the capacitance formed between the sensor and the conductive or non-conductive liquid. Ultrasonic sensors, on the other hand, utilize sound waves to measure distance to the liquid surface, offering non-contact measurement ideal for corrosive or hot environments.
Capacitance sensors, with their ability to operate without direct contact with the liquid, provide a significant advantage in situations where contamination or chemical reaction is a concern. They are particularly adept at handling volatile or corrosive substances, making them a go-to choice in chemical processing, pharmaceuticals, and food and beverage industries. This versatility also extends to their use in bulk solids and slurries, where the material's characteristics can greatly vary. The technology behind capacitance sensors allows for fine-tuning to account for different dielectric constants of materials, offering precise measurements even in challenging conditions.
Ultrasonic sensors, leveraging the power of high-frequency sound waves, excel in environments where traditional sensors falter. Their non-intrusive nature minimizes maintenance and eliminates the risk of sensor contamination or damage, ensuring long-term reliability and accuracy. These sensors are particularly useful for applications requiring level measurement over a range of distances, from small tanks to large storage containers. Adjustments can be made to account for environmental factors such as temperature and humidity, which might affect the speed of sound and ultimately, the accuracy of the measurement. This adaptability renders ultrasonic sensors indispensable in a wide array of industries, including water treatment, oil and gas, and material handling.
Electronic Level SensorsAdvancements in technology have led to the development of optical, radar, and magnetic sensors, which promise precision even in challenging conditions. Optical sensors leverage the light transmission and reflection principles, while radar sensors use electromagnetic waves, unaffected by dust, steam, or pressure variances. Magnetic sensors, employing magnetic floats and reed switch technology, offer a robust solution for continuous level measurement.
Optical level sensors operate based on the principle of light refraction and reflection. These sensors emit a beam of light, usually an infrared LED, towards the liquid level. When the light encounters the liquid surface, the change in the refractive index causes a portion of the light to be reflected back to the sensor. This reflection, or lack thereof, is then used to determine the presence or absence of the liquid at a specific level. Optical sensors are appreciated for their precision and the absence of moving parts, which minimizes wear and tear and enhances reliability. Their non-contact nature makes them ideal for use in sterile environments or in applications where contamination is a concern, such as in the pharmaceutical and food and beverage industries.
Radar level sensors, on the other hand, utilize microwave radar technology to detect the level of liquids. These sensors emit microwave pulses that travel at the speed of light towards the surface of the liquid. A portion of this signal is then reflected back to the sensor, with the time delay between emission and reception of the pulse indicating the distance to the liquid surface. Radar sensors are highly accurate and unaffected by temperature, pressure, or gas vapors, making them suitable for challenging industrial environments. They can operate in extreme conditions, such as high temperatures and pressures, and in the presence of volatile or corrosive substances, ensuring reliable performance in sectors such as oil and gas, chemical processing, and wastewater management. Their versatility and robustness make radar level sensors a preferred choice for continuous level measurement in complex applications.
Varieties and Features of Liquid Level SensorsThe realm of liquid level sensing is rich with a variety of sensors, each designed to meet specific application needs.
- Float Switches: Available in vertical and horizontal configurations, float switches are versatile in application, from sump level control to tank level monitoring. They are economical, simple to install and maintain, and suitable for use in a wide range of liquids. Their compact size and durable construction make them ideal for use in areas with limited space or harsh environments.
- Float switches are commonly employed in various industrious and commercial settings, exemplifying their adaptability and efficient monitoring capabilities. For instance, in wastewater treatment facilities, float switches are integral to managing the levels within treatment tanks, ensuring optimal operations and preventing overflows. Similarly, in the oil and gas industry, these devices play a crucial role in monitoring the contents of storage tanks, helping to prevent spills and facilitating efficient inventory management. Another notable application is within residential contexts, where float switches are used in sump pumps to prevent basement flooding. This broad range of applications underlines the float switch’s esteemed position in providing reliable and straightforward solutions to liquid level measurement and control challenges across diverse sectors.
- Conductive Sensors: Highly efficient at detecting the level of conductive liquids, such as water-based solutions, these sensors combine simplicity and efficiency. They operate either by using two electrodes immersed in the liquid, where the resistance between the electrodes changes as the liquid level rises or falls, or through the use of an electrical field to detect a change in conductivity between two probes when submerged. Conductive sensors are reliable, easy to integrate into control systems, and offer non-intrusive level measurement, making them suitable for a wide array of applications.
- Conductive sensors find their utility in various practical scenarios, reflecting their adaptability and efficiency in level detection tasks. For instance, in the food and beverage industry, they play a pivotal role in ensuring tanks used for storing liquid ingredients maintain optimal levels, thus safeguarding against both shortages and overflows that could disrupt production processes. In chemical manufacturing, conductive level sensors are integral for maintaining precise levels of reactive or corrosive liquids in process tanks, a critical factor for ensuring safety and process efficiency. Furthermore, in water treatment facilities, they assist in monitoring the levels of treatment chemicals in dosing tanks, facilitating the accurate treatment of drinking water and wastewater. These real-world applications underscore the versatility and reliability of conductive sensors in managing the levels of conductive liquids across a broad spectrum of industries, ensuring both process optimization and safety.
- Capacitance Sensors: Distinguished by point level and continuous level versions, these sensors excel in detecting precise level changes across a vast range of liquids. They are versatile and can be used in a variety of tanks, including those with odd shapes or non-metallic structures. Their reliability lies in the ability to adjust their sensitivity according to the dielectric constant of different materials, making them suitable for use in challenging environments.
Capacitance level sensors demonstrate their utility across multiple industrial sectors, leveraging their sensitivity to minute changes in liquid level to ensure operational accuracy and safety. For instance, in the petrochemical industry, these sensors are vital for monitoring the levels of volatile organic compounds and crude oils within storage tanks, preventing spills and facilitating precise inventory management. Their ability to function accurately in the presence of aggressive chemicals makes them indispensable in chemical processing plants, where maintaining correct levels of acids and bases in reaction vessels is critical to process safety and efficiency. Additionally, in the agricultural sector, capacitance sensors are employed within irrigation systems to manage water reservoir levels, optimizing water usage and ensuring the sustainability of agricultural practices. These examples epitomize the broad applicability and reliability of capacitance level sensors in addressing complex liquid level measurement challenges in demanding and diverse environments.
- Ultrasonic Sensors: These sensors employ high-frequency sound waves to determine liquid level measurements. They offer non-contact and non-intrusive level detection, making them ideal for use in hazardous or corrosive environments. They can measure levels over a wide range of distances and are highly adaptable to environmental factors.
- Ultrasonic sensors stand out for their widespread application across various industries, attributed to their non-contact measurement capabilities. In the environmental sector, for example, they are essential for monitoring water levels in rivers and reservoirs, facilitating flood management and water resource planning. The petrochemical industry also benefits from ultrasonic sensors, utilizing them to ensure safe distances are maintained in volatile liquid storage, thus preventing overfills and ensuring worker safety. Furthermore, in the manufacturing realm, these sensors are critical for controlling the levels of liquids in vats and tanks, directly impacting product consistency and quality control. Their ability to accurately gauge levels without coming into contact with the measured substance makes ultrasonic sensors a preferred choice for industries dealing with hazardous materials or extreme conditions, showcasing their versatility and reliability in a plethora of operational contexts.
- Optical Sensors: Utilizing the principles of light transmission and reflection, optical sensors offer precise level detection in a variety of applications. Their non-contact measurement minimizes the risk of contamination, making them perfect for sterile or clean environments like those found in the pharmaceutical and food industries. With no moving parts, these sensors guarantee longevity and reduced maintenance, providing a reliable solution for both point level and continuous level measurement tasks.
- Optical sensors, with their precise and contaminant-free operation, offer extensive utility in environments requiring the highest levels of sanitation and accuracy. For example, in the pharmaceutical industry, these sensors are employed to monitor fluid levels in bioreactors and storage vessels, ensuring the strict control necessary for the production of pharmaceuticals where even minor deviations can compromise product integrity. In the food and beverage sector, optical sensors facilitate the automated bottling process by ensuring containers are filled to the correct levels, thus maintaining consistency and preventing product waste. Furthermore, in semiconductor manufacturing, where the cleanliness of production environments is paramount, optical sensors play a crucial role in liquid level measurement within chemical supply lines, ensuring the precise management of chemicals used in the fabrication process. These scenarios underscore the adaptability and reliability of optical sensors in supporting industries where precision, cleanliness, and efficiency are non-negotiable.
- Radar Sensors: Employing cutting-edge microwave technology, radar sensors offer unparalleled precision in liquid level detection. Their ability to function flawlessly under a wide range of environmental conditions, including extreme temperatures, pressures, and in the presence of vapors or gases, makes them invaluable for applications in harsh industrial settings. Radar sensors are distinguished by their resilience and versatility, catering to continuous level measurement needs across sectors like oil and gas, chemicals, and wastewater treatment without being influenced by the medium's properties.
- Radar sensors' robustness and accuracy are exemplified through their application within the oil and gas industry, where they are employed for gauging levels in petroleum storage tanks under extreme conditions of pressure and temperature. In these environments, radar sensors ensure operational efficiency and safety by providing reliable level measurements, crucial for inventory control and spill prevention. Another notable application is found in the wastewater treatment sector, where radar sensors monitor the levels of various treatment tanks, facilitating the management of waste processing and ensuring environmental compliance. Furthermore, in the chemical manufacturing industry, the deployment of radar sensors enables the precise monitoring of reactive and hazardous chemicals within vessels, playing a pivotal role in maintaining process integrity and worker safety. These real-world scenarios highlight the indispensable value of radar sensors in managing complex industrial processes safely and efficiently.
Each type of sensor comes with its own set of features regarding sensitivity, accuracy, measuring range, and adaptability, allowing for tailored solutions that enhance system performance across industries.
Practical Applications Across Industries

Liquid level sensors play pivotal roles in various sectors, ensuring systems operate smoothly, safely, and efficiently.
- Oil and Water Separation: In the oil industry, sensors monitor separator tanks, ensuring optimal separation efficiency and preventing overflows.
- Food Processing: Ensuring proper levels in beverage tanks or vats, sensors help maintain product consistency and quality.
- Chemical Storage: In chemical plants, sensors monitor storage tanks to prevent spills, ensuring worker safety and environmental protection.
- HVAC Systems: Maintaining levels in cooling towers and boilers, sensors contribute to energy efficiency and system stability.
- Pharmaceutical Manufacturing: Precise level measurement is critical in pharmaceutical production processes, ensuring the correct dosages and mixtures in batch processing and continuous manufacturing setups.
- Agriculture and Irrigation: In farming, sensors can manage water levels in irrigation systems, storage tanks, and reservoirs, optimizing water usage and ensuring crop health during varying weather conditions.
- Wastewater Treatment: Critical for environmental protection, sensors in wastewater treatment plants monitor the stages of treatment to ensure efficient processing and compliance with regulatory standards.
- Marine and Shipping: Sensors are used in ballast tanks and fuel monitoring to maintain balance and efficiency in marine vessels, contributing to safe and economical shipping operations.
- Mining: In the mining industry, sensors help manage slurry levels and detect water in sumps, crucial for efficient extraction processes and worker safety in challenging underground environments.
Despite their wide-ranging applications, implementing liquid level sensors presents challenges such as ensuring accuracy in harsh environments, achieving compatibility with various media, and maintaining sensors over their operational life. Innovations in materials, design, and technology, like IoT integration and predictive analytics, are paving the way for overcoming these obstacles, enhancing sensor longevity and performance. With the continuous development of advanced sensors, industries can leverage accurate and reliable level measurement solutions to optimize processes, reduce waste, enhance safety, and increase efficiency. As technology continues to advance, liquid level sensors will continue to play a crucial role in various sectors essential for our daily lives. From managing critical operations in industrial settings to promoting sustainable practices in agriculture and protecting the environment, liquid
Looking Ahead: Trends and Future Projections

The future of liquid level sensor technology is marked by trends toward increased connectivity, miniaturization, and intelligent analytics, driving toward predictive maintenance and operational excellence. The integration of sensors with IoT platforms heralds a new era of data-driven decision-making, optimizing processes, and preempting system failures before they occur, signifying a proactive rather than reactive approach to industrial management.
The integration of Internet of Things (IoT) technology into liquid level sensors signifies a paradigm shift in how industries monitor and manage liquid assets. By connecting sensors to the IoT, data collected from various points across a facility can be centralized, offering an unprecedented overview of operational status in real time. This connectivity allows for the seamless transmission of data to cloud-based platforms, where advanced analytics can process and interpret the information. In practical terms, this enables predictive maintenance, where potential issues such as leaks or equipment failures can be identified before they escalate into major problems, thus minimizing downtime and maintaining continuous operation. The IoT integration also facilitates remote monitoring, allowing operators to track liquid levels from anywhere, enhancing the flexibility and responsiveness of management strategies.
Furthermore, IoT-enabled liquid level sensors contribute significantly to the optimization of resource usage and energy efficiency. Through continuous monitoring and data analysis, systems can more precisely control the use of liquids in processes, reducing waste and ensuring that resources are utilized in the most efficient manner possible. For example, in agriculture, IoT-connected sensors can optimize irrigation schedules based on the actual water levels in storage tanks and soil moisture content, leading to more effective water use and healthier crop growth. In industrial settings, such as chemical manufacturing or oil refining, the ability to closely monitor and adjust liquid levels in real-time can lead to more consistent product quality and safer working conditions. The integration of IoT into liquid level sensing technology is not just an enhancement of existing capabilities; it's a transformation that drives industries towards more sustainable, efficient, and productive operations.
ConclusionIn conclusion, as we chart the course of liquid level sensor technology, it's clear that the depth of its impact is profound, permeating every facet of industrial operations. By staying abreast of technological advancements and understanding the nuances of sensor applications, industry professionals can harness the power of these indispensable tools, navigating the complexities of modern industrial landscapes with confidence and precision.
For more in-depth insights into the latest advancements in liquid level sensor technology and how it can transform your industry, visit ACT Sensors. Discover a range of innovative solutions designed to meet the demands of modern applications. Take the first step towards enhancing your operational efficiency and safety by exploring our cutting-edge products and services. Collaborate with us to leverage the power of intelligent sensor technology and drive your business forward into a more sustainable, productive future.