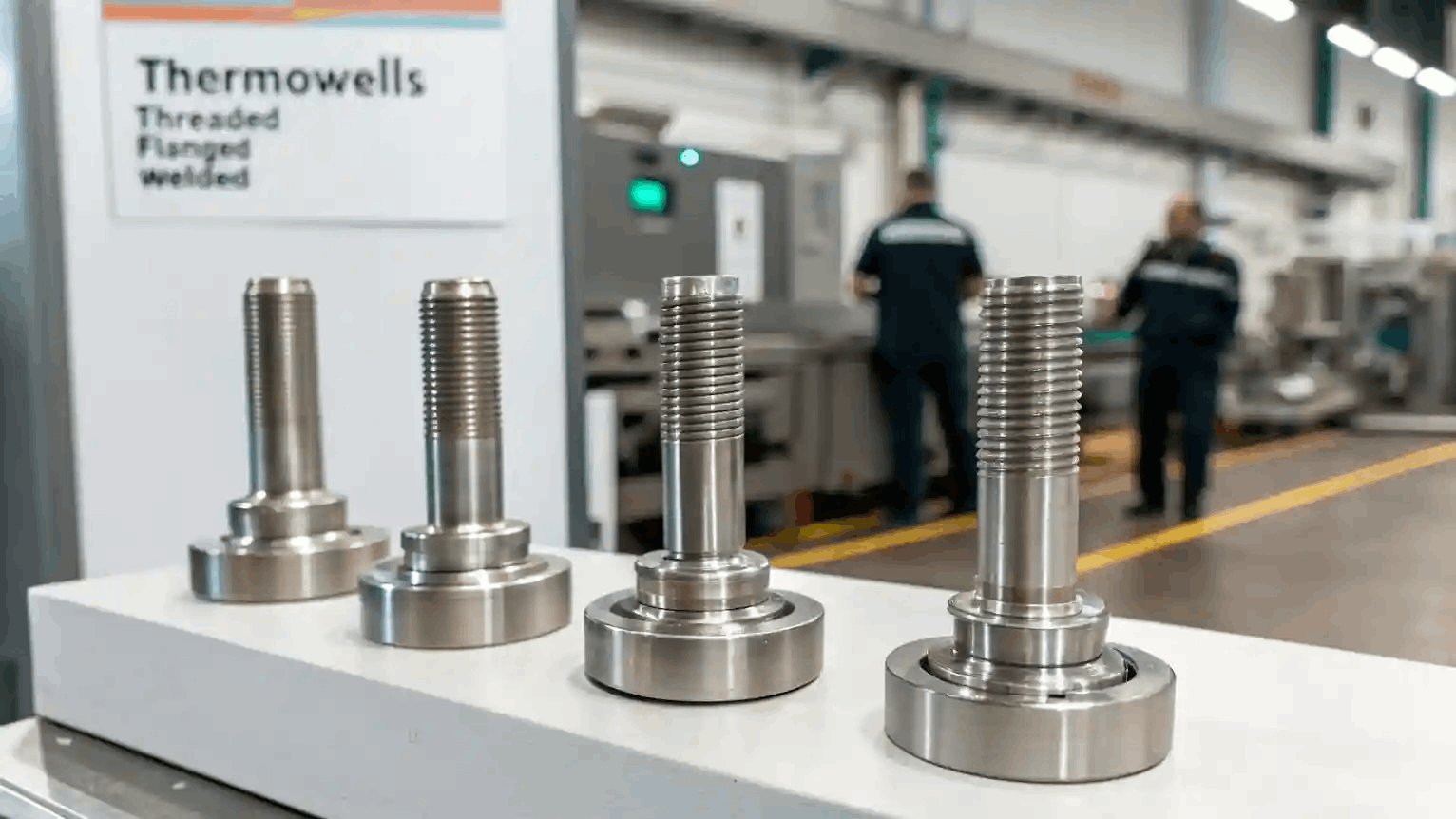
What Are the Different Types of Thermowells?
Introduction to Thermowell Geometry
Thermowells come in three primary designs: straight, tapered, and stepped. Each offers unique advantages based on thermowell design. The choice you make depends on factors such as strength, response time, and suitability for your specific process environment.
The geometry of a thermowell influences more than just its appearance. It determines critical characteristics like mechanical strength, resistance to vibration, and sensor response time. Whether you're managing a chemical process or a flow system, understanding these distinctions can guide you to a better choice.
Purpose of Different Shapes
-
Straight thermowells prioritize durability and are preferred for handling static systems or conditions with minimal flow.
-
Tapered thermowells balance strength and responsiveness in high-velocity or vibration-heavy environments.
-
Stepped thermowells reduce probe tip diameter to improve sensitivity, ensuring faster response times at the possible expense of some durability.
By understanding these shapes, you’ll be better prepared to evaluate thermowell performance and select the one that best aligns with your requirements.
Straight Thermowells
The straight thermowell is a classic design favored for its simplicity and robustness. Its cylindrical structure maintains a consistent diameter from top to bottom.
Design Characteristics
Straight thermowells are simple and easy to produce. This makes them cost-effective, particularly for applications without demanding operational needs. Their consistent design provides durability, ensuring they hold up well under sustained pressure.
Benefits and Best-Fit Applications
-
Ideal for static or low-velocity environments.
-
Excellent for processes requiring high durability without much vibration.
Limitations under High-Velocity Flow
While durable, the straight thermowell may struggle when exposed to high-velocity flow. The lack of tapering increases drag forces, which can lead to stress and deformation. For more fluid-intensive systems, other shapes may offer better performance.
Tapered Thermowells
Tapered thermowells are designed to widen the range of applications a thermowell can handle. Their narrowing structure improves adaptability and protection in more dynamic or aggressive conditions.
Overview and Functional Advantages
The tapered thermowell tapers from a wider base to a narrower tip. This conical shape enhances its ability to resist drag and vibration. Not only does this reduce the mechanical load on the well itself, but it also lowers wear and tear on the temperature sensor.
Resistance to Vibration and High Flow
One crucial advantage of the tapered thermowell is its vibration resistance. These are well-suited for high-flow applications that demand resilience against turbulent conditions. By reducing drag, they also last longer under such harsh environments, safeguarding both the thermowell and the sensor within.
Common Industrial Applications
Tapered designs are commonly used in:
-
Petrochemical facilities
-
Power generation plants
-
High-speed flow systems requiring precise temperature control
Stepped Thermowells
A stepped thermowell combines aspects of the straight and tapered designs, offering speed and accuracy through its unique shape.
How Does the Step Improve Response Time?
The stepped thermowell transitions to a smaller tip diameter near the sensor probe. This smaller tip interacts more directly with the fluid or gas, allowing it to respond to thermal changes faster. Faster thermal response is often vital in sensitive operations.
Considerations for Accuracy vs Durability
While the stepped thermowell excels at offering quick temperature readings, it sacrifices some structural durability. When working with heavily corrosive substances or extreme pressures, this trade-off becomes a crucial consideration in your thermowell selection guide.
Comparison Table: Straight vs Tapered vs Stepped
The chart below provides a high-level thermowell shape comparison in terms of performance, cost, and application fit.
How to Choose the Right Thermowell Type
Selecting the appropriate thermowell requires analyzing various factors. Each thermowell design has specific strengths that make it ideal for different processes. Below are some key considerations:
Fluid Dynamics, Installation Constraints, and Process Criticality
-
Fluid dynamics – Understand flow velocity and turbulence in your operating environment.
-
Installation space – Consider the physical fit and constraint of the thermowell.
-
Process criticality – Evaluate how much faster response time or vibration resistance matters to your operation.
Industry-Specific Recommendations
-
Chemical processing: Opt for straight thermowells in low-flow reactors; tapered thermowells for pipelines.
-
Oil & gas: Use tapered thermowells, especially for upstream conditions with high vibration.
-
Power plants: Leverage stepped thermowells for turbine monitoring, where fast response time improves operational control.
Carefully addressing these needs ensures improvements in sensor longevity, measurement accuracy, and operational safety.
Conclusion
Choosing the right thermowell is crucial for ensuring accurate temperature readings, protecting your sensors, and optimizing performance in industrial processes. Whether you need the durability of a straight thermowell, the vibration resistance of a tapered design, or the quick response time of a stepped thermowell, selecting the right type can make all the difference. For expert advice or to compare thermowell types, contact ACT Sensors or download our Thermowell Type Comparison Chart today.