
The Complete Guide to Thermowells: Types, Applications, and Best Practices

Thermowells are essential components in industrial temperature measurement setups, serving as a protective barrier for temperature sensors in a wide range of environments. By isolating sensors from process fluids, pressure, and harsh environmental conditions, thermowells help prevent damage, increase the longevity of equipment, and ensure consistent and accurate temperature readings. Their robust design allows sensors to be removed and replaced without interrupting the process, making them indispensable in industries such as oil and gas, chemical processing, power generation, and more.
Thermowell design plays a critical role in ensuring effective temperature management systems. Factors such as material compatibility, process pressure, fluid velocity, and installation depth must all be carefully considered to optimize performance and reliability. This guide will explore the different types of thermowells, including threaded, flanged, and welded designs, along with their specific applications. Additionally, it will cover best practices for thermowell selection based on process requirements and installation techniques to maximize accuracy and durability. Understanding these factors will help ensure your temperature measurement systems perform efficiently and reliably in even the most demanding environments.
What is a Thermowell and Why Is It Important?
A thermowell is a cylindrical tube designed for temperature sensor protection, shielding devices like thermocouples or resistance temperature detectors (RTDs) from harsh environments. It allows sensors to function effectively by safeguarding them from pressure, flow, and corrosive substances.
By providing temperature sensor protection, thermowell applications are essential across industries such as oil and gas, food processing, chemical manufacturing, and power generation, where durability and accuracy are critical. These protective devices act as a barrier between sensors and challenging process conditions like high pressure, corrosive materials, or extreme temperatures. A well-designed thermowell ensures reliable, precise temperature readings and minimizes disruptions by allowing sensor maintenance or replacement without halting operations, making them vital for efficiency and safety in demanding environments.
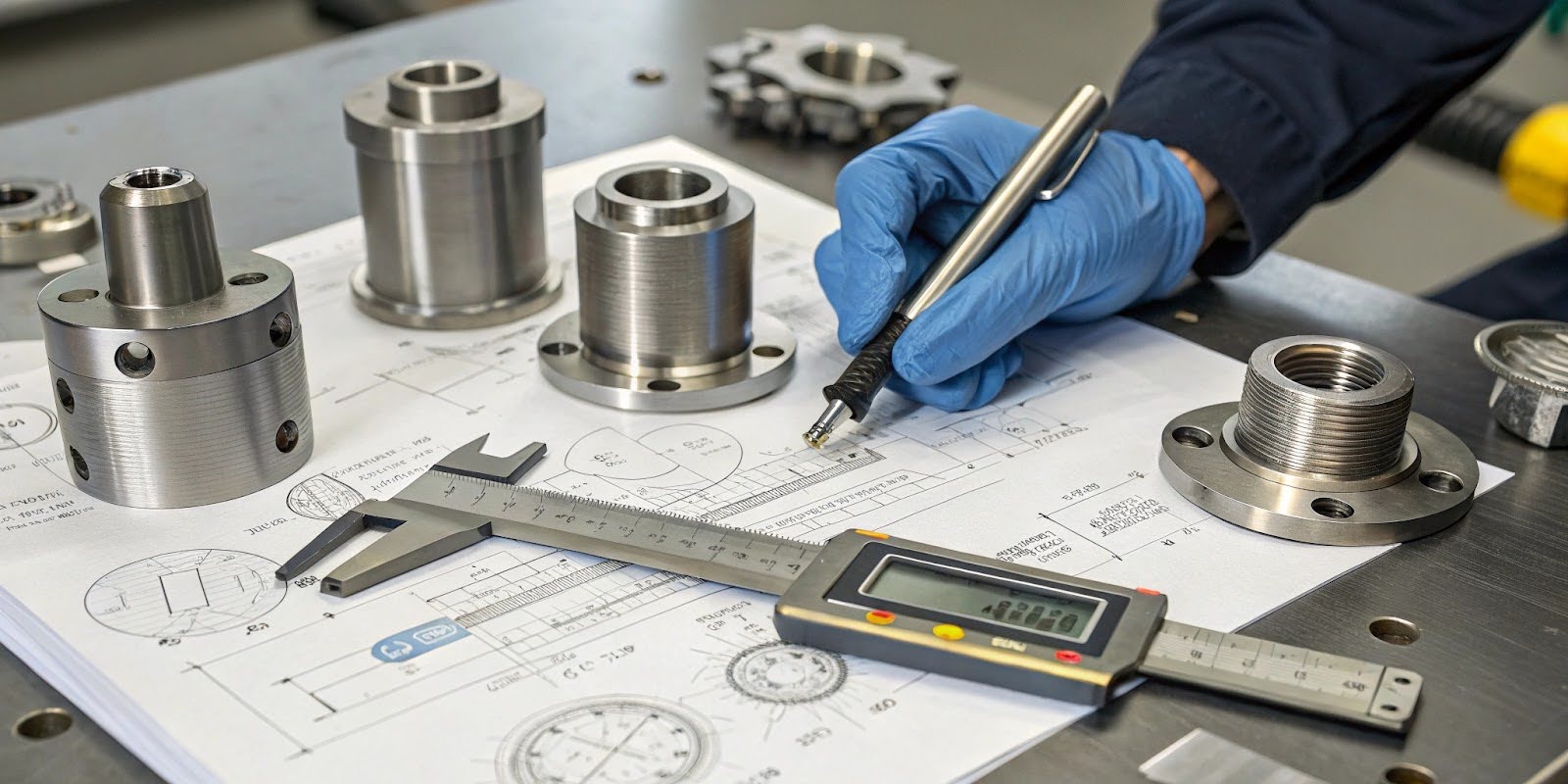
Understanding the Different Types of Thermowells
Thermowells come in various types, each suited to specific applications and designs.
Straight Thermowell A straight thermowell has a uniform diameter from base to tip. It’s commonly used in low-flow or low-pressure environments due to its simplicity and ease of manufacturing.
Tapered Thermowell
A tapered thermowell narrows toward the tip, increasing strength and reducing fluid resistance. This design minimizes vibration from wake frequency, making it ideal for high-pressure, high-velocity applications.
Stepped Thermowell
A stepped thermowell tapers near the tip, improving response time while maintaining strength. It’s perfect for applications needing fast, accurate temperature readings.
How Geometry Affects Performance
The shape and size of a thermowell impact its response time, vibration resistance, and heat transfer. Factors like wall thickness, length, and tip design are critical for optimal performance in specific conditions.
Thermowell Materials and Design Standards
Thermowell Design
Proper thermowell design ensures performance and safety. Key factors to consider include:
Wake frequency calculation to avoid resonance and thermowell vibration, which can lead to failure.
Structural durability to endure both pressure and high-temperature fluctuations.
Compatibility between the thermowell materials and the temperature sensor for consistent readings. Conformity with thermowell standards (ASME, ISO).
Compliance with ASME standard thermowell (PTC 19.3 TW) and ISO 9001, is essential to ensure safety, reliability, and accurate performance in temperature measurement systems. Adhering to these standards helps guarantee that thermowells are designed and installed correctly to withstand process conditions like pressure, vibration, and thermal stress.

Thermowell Materials
The choice of thermowell materials directly impacts durability and compatibility. Popular materials include:
Stainless Steel for corrosion resistance.
Hastelloy for applications in chemically aggressive environments.
Monel for high-temperature operations and saltwater exposure.
Selecting the correct material ensures that the thermowell meets the demands of its environment without degradation or failure.
Thermowell Applications in Various Industries
Industrial Thermowells
Their applications are widely used across industries, including:
Oil and Gas
Thermowells protect temperature sensors in pipelines, refineries, and drilling sites. Built to handle high pressure, corrosive environments, and extreme heat, they ensure accurate readings for safe, efficient operations.
Power Generation
In power plants, thermowells ensure precise temperature measurements in boilers, turbines, and other equipment. They shield sensors, enabling continuous monitoring to optimize performance, prevent overheating, and maintain system safety.
Food and Beverage
Thermowells ensure strict temperature control in processes like pasteurization, fermentation, and sterilization. By protecting sensors from food and cleaning agents, they ensure hygiene, accuracy, and compliance with quality standards.
Chemical Processing
In chemical plants, thermowells shield sensors from harsh, reactive substances in processes like distillation and mixing. Their durability and corrosion resistance ensure reliable monitoring, process efficiency, and reduced equipment damage.
The core function of thermowells lies in providing temperature sensor protection while ensuring accurate and reliable readings in various industrial applications. By acting as a protective barrier, thermowells shield sensors from harsh environments, such as extreme temperatures, pressure, or corrosive materials, which could otherwise damage them. Additionally, thermowells allow for easy maintenance and replacement of sensors without the need to shut down equipment, significantly reducing downtime and minimizing disruptions to operations. This makes them an essential component in industries where precision and efficiency are critical.
Installation and Wake Frequency Considerations
Proper thermowell installation is crucial for reliable performance. Here are best practices to avoid thermowell failures:
Orientation: Install them perpendicular to the flow to minimize wear and avoid thermowell vibration-related issues.
Wake Frequency Testing: Confirm that the wake frequency of the flow does not resonate with the thermowell to prevent vibration-induced damage.
Sealing: Ensure proper sealing between the thermowell and equipment to keep contaminants out.
By following these steps, you enhance the lifespan and functionality of both the thermowell and the temperature sensor.
How to Select the Right Thermowell
When approaching thermowell selection, it's important to evaluate key factors to ensure safety, efficiency, and compatibility with your system. Start with a thermowell design checklist:
Media type: Identify the medium being measured to select materials that can withstand corrosion, chemical exposure, or other interactions.
Flow velocity: Consider the flow rate the thermowell will encounter, as higher velocities can cause vibrations that may impact performance or durability.
Pressure: Determine the maximum operating pressure to ensure the thermowell can handle the application without failure.
Sensor compatibility: Ensure the thermowell design works seamlessly with your RTD or thermocouple sensors for accurate temperature readings.
Balancing these factors with your operational needs will help you find a thermowell that performs reliably in your specific application.
The Importance of Choosing the Right Thermowell
Selecting the appropriate thermowell is critical for ensuring sensor longevity and maintaining operational safety in industrial environments. The choice of thermowell type and material must align with the process conditions, such as temperature, pressure, and media compatibility, to prevent premature failure. Proper analysis of wake frequency is equally vital to avoid resonance, which can lead to structural damage or system downtime. Equally important is correct installation, as improper mounting can compromise the accuracy of temperature measurements and the overall integrity of your system.
Need help selecting the right thermowell for your plant? Contact ACT for a free consultation or download our Thermowell Selection Guide.