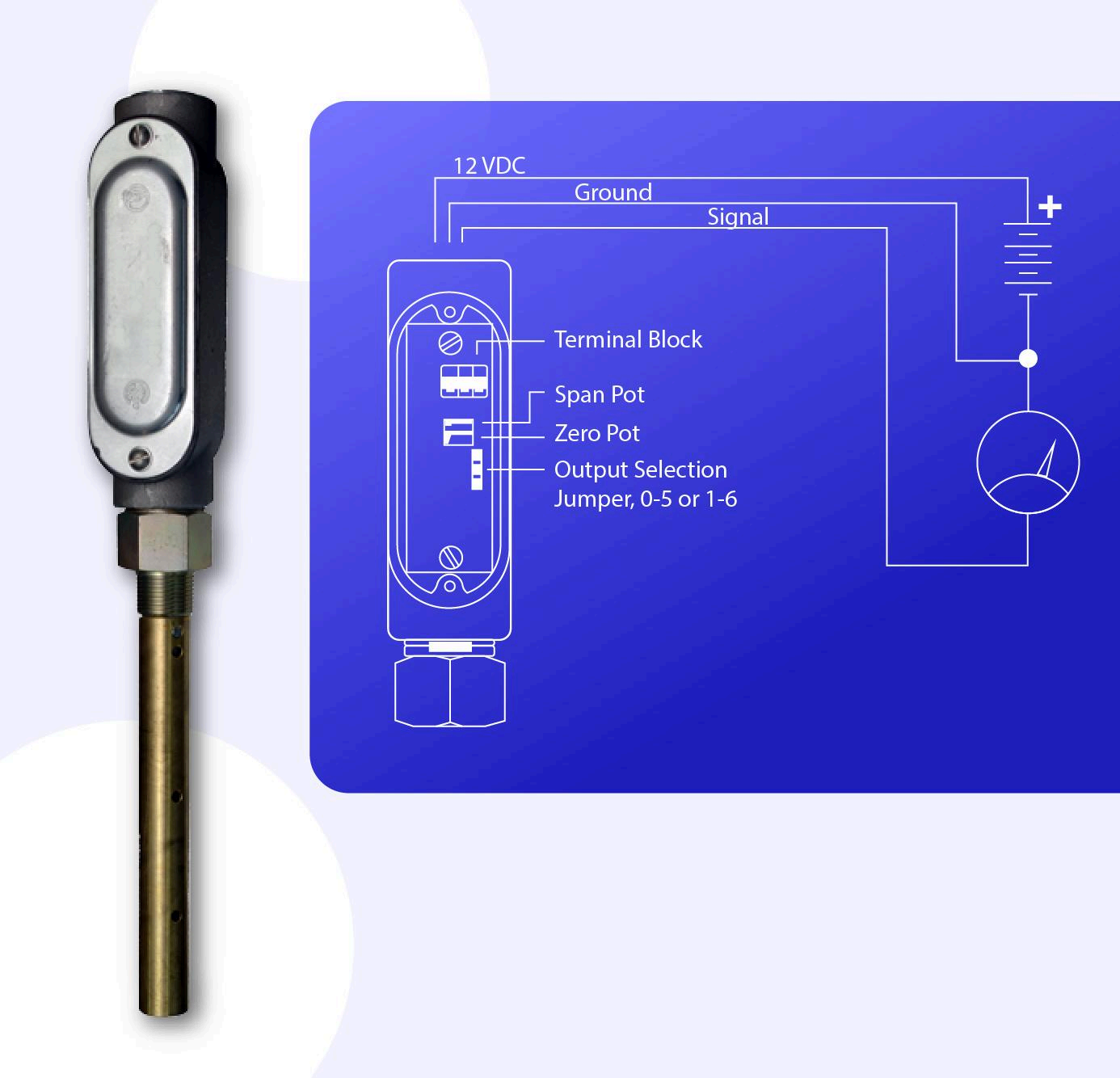
Mastering Level Measurement: A Guide to Sensor Technology with ACT Sensors
In countless industrial, commercial, and even consumer applications, the precise measurement and monitoring of liquid and solid levels are paramount. The fundamental level sensor working principle across all types involves converting a physical material level into a measurable electrical signal. From ensuring operational efficiency in manufacturing plants to safeguarding critical equipment like sump pumps, the right level sensor technology is crucial. ACT Sensors stands at the forefront of providing robust and reliable level sensing solutions tailored to diverse needs across the USA, often forming key components in act advanced process control systems.

Understanding the Fundamentals: What Are Liquid Level Sensors?
A liquid level sensor is a device designed to detect the level of liquids, fluids, and sometimes granular solids, within a container or natural environment. These sensors can trigger alarms, initiate control actions (like starting or stopping a pump), or provide continuous level data. The applications are vast, ranging from simple water level sensor applications in tanks to complex fuel level sensor systems in automotive and aerospace, or an oil level sensor in industrial machinery. Understanding how do capacitive sensors work, for example, unlocks solutions for many challenging applications.
The Rise of Advanced Sensing: Spotlight on Capacitive Level Sensors
ACT Sensors specializes in a variety of sensing technologies, with a particular strength in capacitive level sensor technology. The core of the capacitive level sensor working principle lies in its ability to measure changes in capacitance. So, how do capacitive sensors work exactly? A capacitive level sensor, often configured as a probe (like a capacitance fuel probe in fuel tanks), forms one plate of a capacitor, while the vessel wall (if conductive) or an auxiliary reference electrode forms the other. The substance being measured (liquid or solid) acts as the dielectric material between these plates. As the level of this substance changes, the amount of dielectric material between the plates changes, which directly alters the overall capacitance of the system. The higher the dielectric constant of the material, the greater the change in capacitance for a given change in level. This change in capacitance is then electronically measured and converted into a level reading, which can be an analog signal or a switched output. This signal can be utilized by various electronic level control (ELC) systems, some of which might be designated by specific industry classifications like `elc 1` components, for automated management.
These sensors are highly versatile and can be used for both point level detection (like a liquid level switch) and continuous level sensor measurement. They are often preferred for their ability to function as a non contact level sensor when measuring through non-metallic tank walls, or with minimal contact. This makes them suitable for aggressive media or applications requiring high hygiene standards. ACT Sensors offers capacitive water level sensor options that are robust and reliable.
Navigating the Options: Capacitive vs. Ultrasonic vs. Optical Sensors
Choosing the right level sensor involves understanding the strengths and weaknesses of different technologies, each with its distinct level sensor working principle. This is especially true when considering harsh conditions, the need for direct contact, or sensitivity to environmental factors like dust and moisture.
- Capacitive Level Sensors: As discussed, these are excellent for a wide range of liquids and some solids, thanks to their adaptable capacitive level sensor working principle. They can be designed for direct media contact or as non contact level sensors for non-metallic tanks. They are generally unaffected by foam or vapor if properly calibrated. ACT Sensors provides leading capacitive level sensor solutions, including specialized capacitance fuel level sensor designs.
- Ultrasonic Level Sensors: These are popular non contact level sensor options. An ultrasonic level sensor emits high-frequency sound waves that reflect off the surface of the medium. The time taken for the echo to return is used to calculate the level. Ultrasonic water level sensors are common, but performance can be affected by turbulence, foam, heavy vapors, or dust.
- Optical Level Sensors: These sensors use infrared light. For point level detection, a change in the refractive index when the sensor tip is submerged alters the light path, triggering a switch. Optical level sensors are compact and precise but require direct contact and can be susceptible to coating or fouling.
- Radar Level Sensors: Similar to ultrasonic, radar level sensors use electromagnetic waves. They are robust non contact level sensors, less affected by temperature, pressure, vapor, or dust compared to ultrasonic, making them suitable for challenging tank level sensor applications.
Exploring Key Sensor Types and Their Roles
Beyond the comparative overview, let's delve into some specific types widely used across industries, all part of the comprehensive offerings from ACT Sensors.
The Ubiquitous Float Switch
The float switch is one of the oldest and simplest liquid level switch technologies. It typically involves a buoyant float containing a magnet that rises and falls with the liquid level, actuating a reed switch. They are cost-effective and reliable for point level detection. Common applications include:
- Sump Pump Float Switch: Essential for activating sump pumps to prevent basement flooding. A sump pump float switch replacement is a common maintenance task.
- Bilge Pump Float Switch: Used in marine applications to control bilge pumps.
- Tank Level Switch: For high or low-level alarms in various storage tanks.
- Magnetic Float Switch: A common design principle for many float switch types.
This type of float level sensor is valued for its simplicity and direct action.
Versatile Applications Powered by ACT Sensors Technology
The diverse range of level sensor technologies, including advanced capacitive level sensors and reliable float switches, enables ACT Sensors to cater to a multitude of sectors. Precise level monitoring is critical in:
- Manufacturing: Monitoring coolants, lubricants (oil level sensor), and raw material levels, often integrated into act advanced process control for optimized production.
- Food & Beverage: Ensuring consistent ingredient levels in hygienic environments, often utilizing capacitive level sensors.
- Automotive: Critical for capacitive fuel level measurement using a capacitance fuel level sensor or capacitance fuel probe. Also essential for engine oil level sensor monitoring and coolant reservoirs. A reliable fuel tank level sensor is key for accurate fuel gauges.
- Pharmaceutical: High-purity applications requiring precise, often non contact level sensor measurement.
- Water Management: From water tank level sensor applications in municipal systems to sump pump float switch control in residential buildings.
ACT Sensors provides robust industrial level sensor solutions that ensure efficiency and safety across these varied applications. Whether you need a continuous level sensor for process control or a simple water level switch for an alarm, we have the technology.
Why Choose ACT Sensors for Your Level Sensing Needs in the USA?
At ACT Sensors, we combine cutting-edge technology with deep application expertise. Our commitment is to provide:
- Precision and Reliability: Our sensors, from advanced capacitive level sensors to dependable float switches, are built for accuracy and longevity. Understanding the capacitive level sensor working principle allows us to optimize them for your needs.
- Tailored Solutions: We understand that one size doesn't fit all. We work with you to identify the optimal liquid level sensor, capacitance fuel level sensor, or tank level sensor for your specific medium and environment through our custom product offerings.
- Expert Support: Our team is ready to assist with selection, integration, and troubleshooting, ensuring our sensors seamlessly integrate into your act advanced process control frameworks.
- Comprehensive Range: Whether it's a non contact liquid level sensor for harsh chemicals, a precise capacitance fuel probe for mobile applications, or a standard water level sensor, our portfolio is extensive.
For industries across the United States requiring dependable level sensor technology that enhances act advanced process control, ACT Sensors is your trusted partner. Contact us today to discuss your application and discover how our liquid level sensor solutions, including premier capacitive level sensor options and robust capacitance fuel level sensor units, can optimize your operations.